Hope, you’ve already read about photogrammetry 3d scanner features and ready to get some more information about creating high-quality scanned 3d model.
What affects the quality of scanned 3d model?
The accuracy of raw 3d prototype and final 3d model depends on many factors. In short, here are 3 main of them:
- Hardware. Defined by design specifics and technical features of the 3d scanner.
- Properties of the scanned object. The surface texture, presence and relative position of any repeating elements, the state of the object.
- Software. Errors within the used math methods of image processing, their format, as well as the specified calculation accuracy.
- Operator’s skill level needs to take into account. The operator ensures the correct relative position of the object and the scanner.
Let us look at how these facts effect the quality of scanning 3d model. Both in positive and negative ways.
Technical features of 3d scanner
The quality of 3d model relates to the next crucial features of 3d scanner:
- The lightning situation must be a diffuse, steady and constant;
- The resolution of the digital cameras. The higher this indicator, the more key points are present. Thus, the accuracy of the model is higher;
- Automatic camera focus for upper sharpness. Focus retention during shooting. If possible, the optical system and the matrix should be parallel to the surface of the object. It is greatly reduces the chance of distortion;
- Color coding and texture capture features.
- The upper size of the object is from 10 to 3000 mm (up to 5000 mm in certain models).
- Scanning time of at least one second.
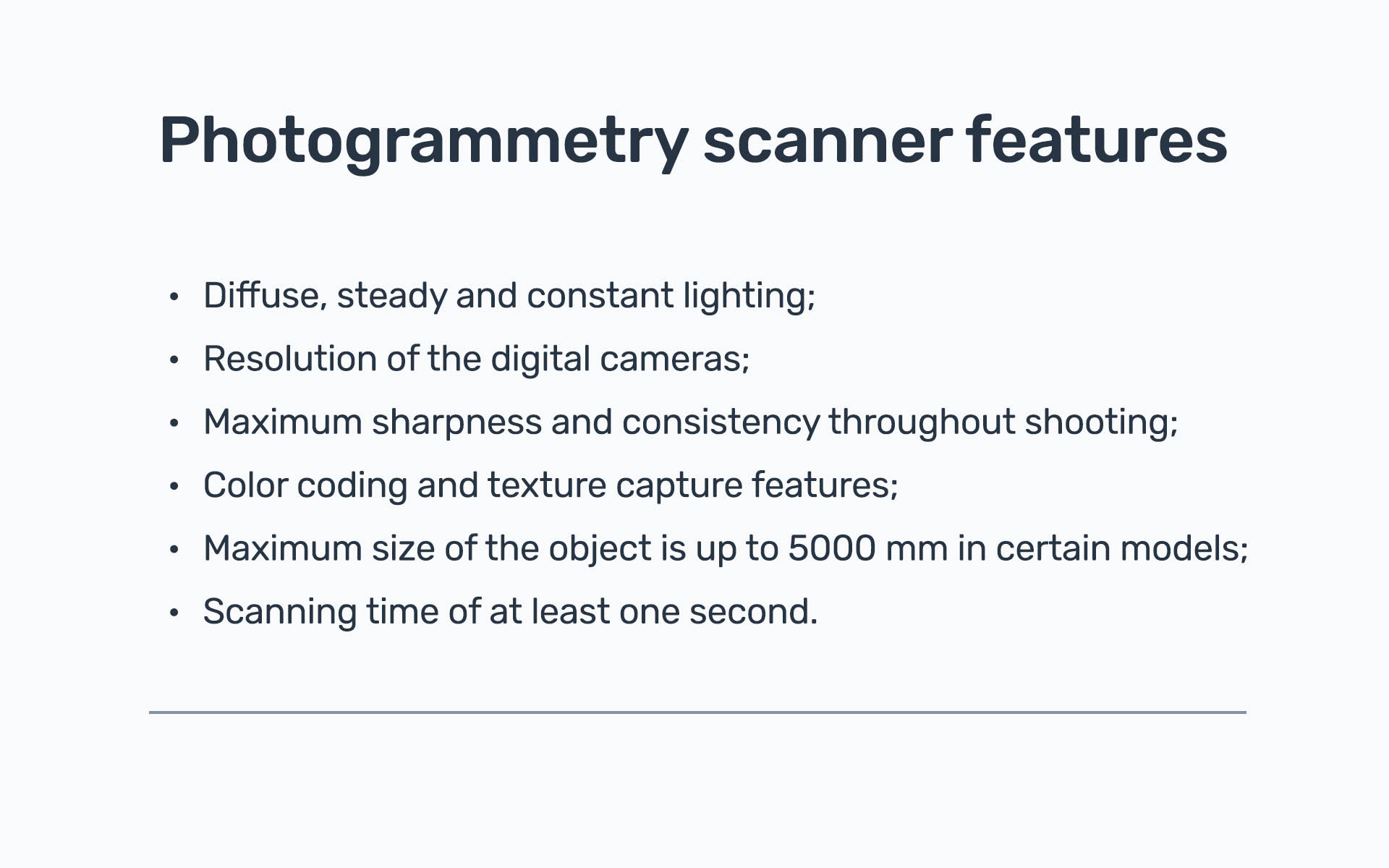
Scanned object requirements
To ensure a high quality scanning, it is required to ensure a dim, diffuse lighting and the fixed, static position. So, in order to achieve this, both the platform with ready-to-scan object on it and the 3d scanner must be secured against any vibration.
And the scanned object must meet certain requirements.
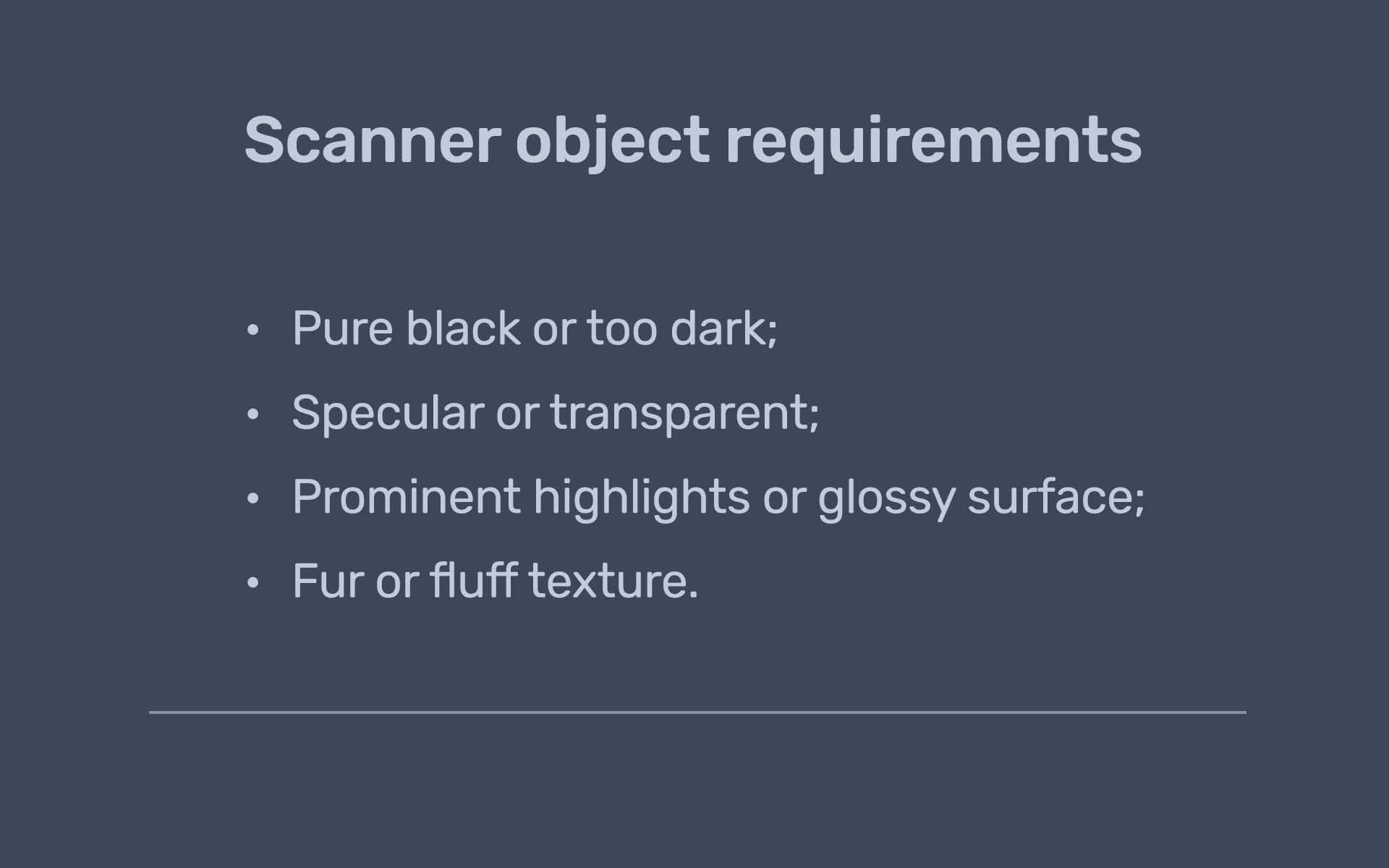
Above all it is good to mat glossy surface. It reduces the negative impact during scanning the object. For this, it is well to use special aerosols. After having dried, they form the finest coating of white powder over the surface. However, hard to scan are objects with fine details, fine cut, deep grooves, through-holes or closed holes.
Points alignment technology
During stage of the process, 3d model creates from a set of partially overlapping stereo images. In order to “stitch” geometry together, the special geometric features of the surface are referred to.
At times, markers can be used. Markers should be located on the object in a chaotic manner. Without forming any straight lines or clear rows. Thus, scanning system captures position of the key points with upper accuracy. In this way, it is possible to minimize distortion when combining fragments of images. Mostly when dealing with extended or large objects. For most design tasks, accuracy is not the only one main factor. Also good to pay attention to noise reduction and fine detail capture.
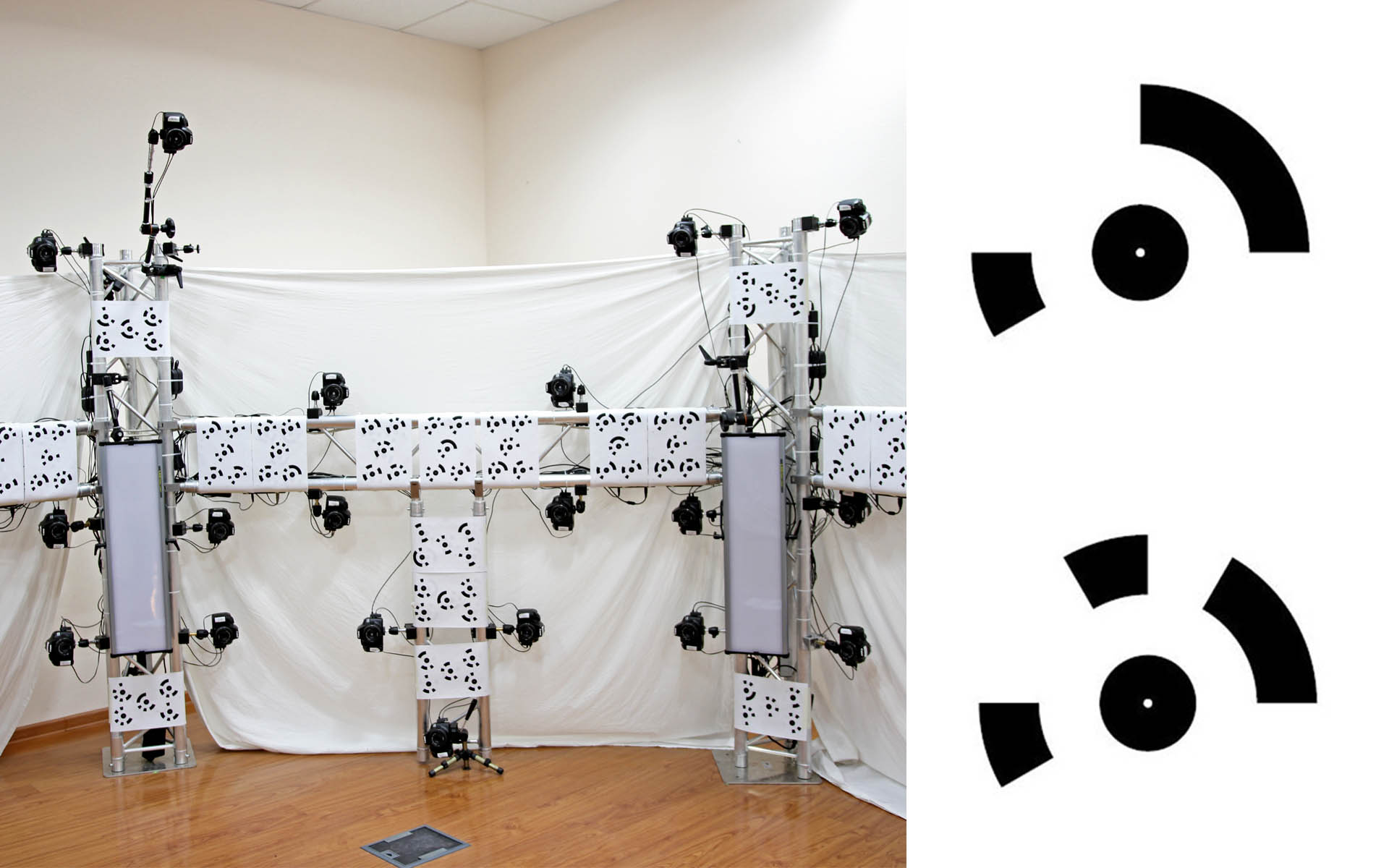
Read more about 3d models production in article Turn-key scanned 3d model: production, prices.
Comments
No comments yet.