A photogrammetry 3d scanner can create 3d products of the highest quality. Reaching accuracy occurs by utilizing special equipment. Not to mention, the specific algorithm for processing the acquired data.
A 3d scanner is a device for shooting objects from multiple angles. Features of the equipment has certain requirements. Thus, the accuracy of this process is much affected by them.
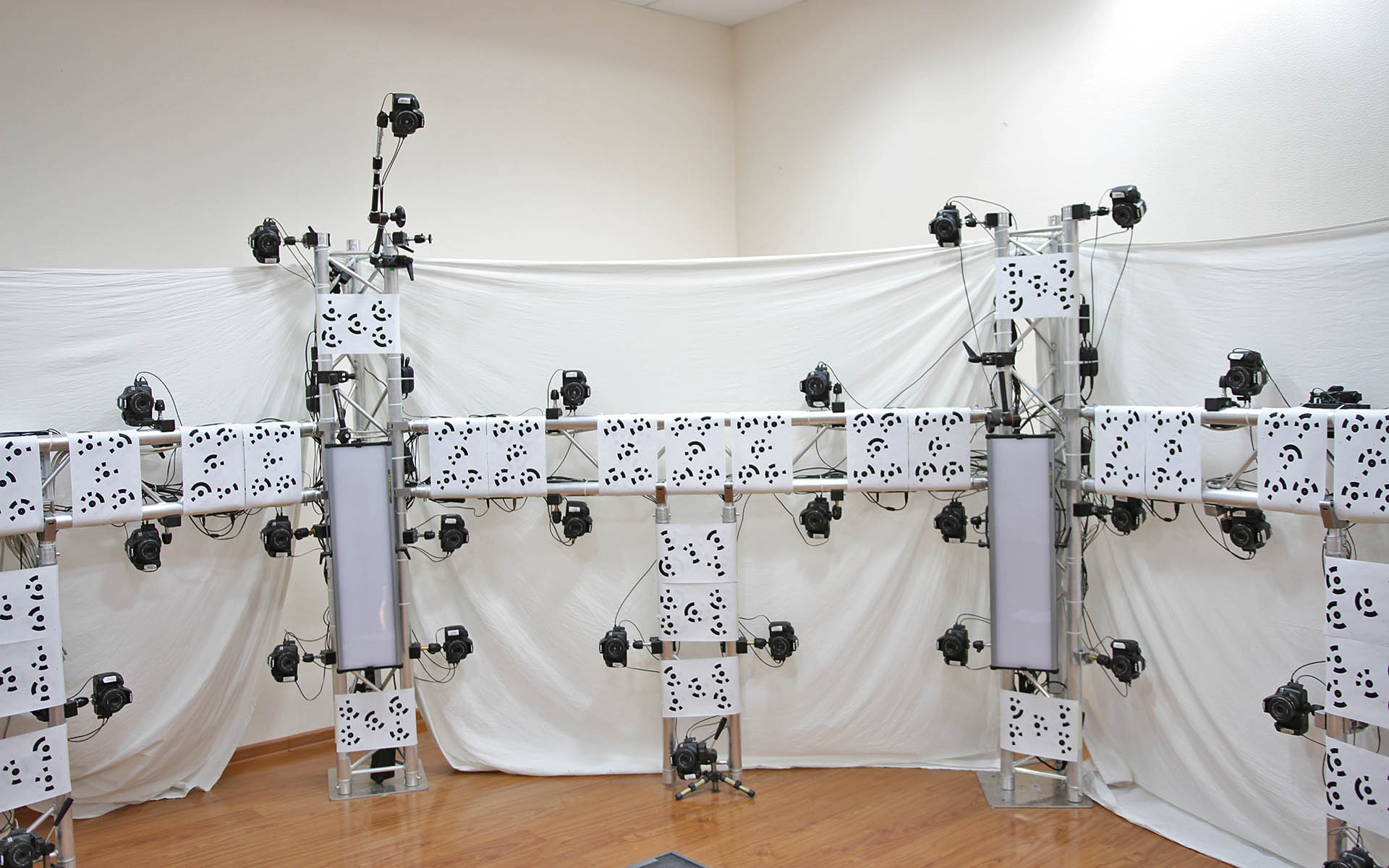
What is a photogrammetry 3d scanner?
A 3d scanner is a hardware system. It consists of the following devices:
- Digital cameras set at a certain distance from each other;
- A flash, mainly LED. It is needed for high-quality scanning of a surface texture;
- A structured light source. Usually, it is a powerful LCD floodlight.
How to obtaining an image with photogrammetry 3d scanner?
So, here are main features that help to get 3d prototype model:
- The scanning system uses the same principle as does the human vision. Binocularity.
- At times technology requires special markers. They are round, either magnetic or with a self-adhesive base. Next, there is a special platform for placing object and the process begins.
- The digital cameras are capturing the object from multiple angles, with overlap of stereo images.
- Cameras have sync system with each other. So, they take a series of simultaneous shots of the object.
- Special file stores the position of the cameras in space. Namely, the exact coordinates, the height, the tilt angle and the rotation angle.
- PC saves acquired data array. Then 3d graphic software processes this data. Thus, it detects related data points and similarities in color data. Using points alignment technology these points turn into key points.
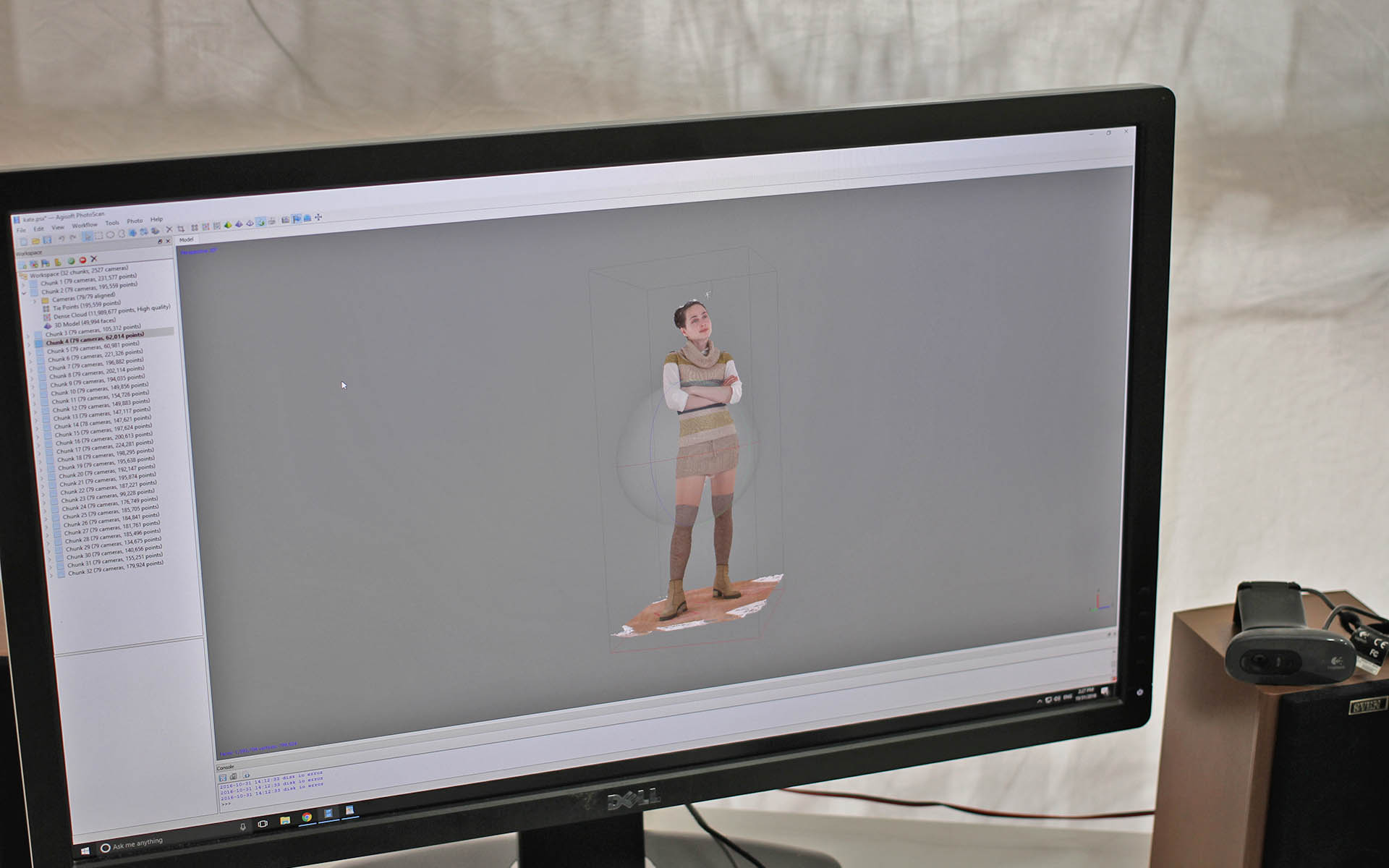
After processing stereo images, the software forms a point cloud. Special algorithms convert these points into a 3d model. So, the surface of the model consists of many polygons.
At the final stage, the 3d figure looks transformed and unwrapped into a plane. At the same time, the position of each point is set on. The color of each point codes in line with the original photo.
The triangulation method
During the generation of a 3d object, it is good to ensure the properties preservation of the scanned object. Namely, its 3d volume, surface texture and relative positions of forming elements. There are two factors to achieve this. First, the position of the spaced cameras of the 3d scanner, relative to space. Second, the depth of field (DOF) values. Then, the key points are converted into a set of triangular polygons. Thus, the process is called triangulation.
Read more about scanned 3d models production in article How to create a high-quality scanned 3d model?
Comments
No comments yet.